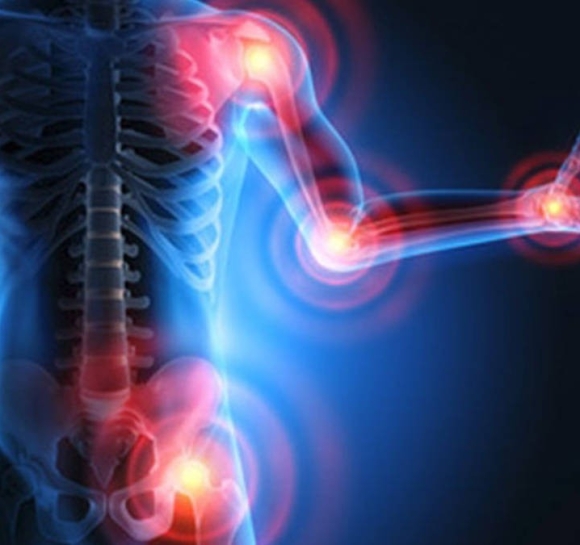
What are the solutions for reducing MSDs (Musculoskeletal Disorders)?
A major source of concern for employers, MSDs are a complex, multi-faceted phenomenon. In this guide, you'll find resources for :
- Reduce workstation-related MSDs and manual handling
- Preventing storage equipment-related MSDs
- Financing your prevention project
What are the symptoms of RSI?
MSDs are conditions that can affect muscles, joints, ligaments and other soft tissues. The symptoms of MSDs can affect several areas of the body, depending on the nature of the movements performed, but the back remains the most frequently cited painful area:
- Pain and/or stiffness: the most frequent symptom of MSDs. It can be localized to a specific spot, or spread along a muscular or articular area, limiting a person's range of movement.
- Tingling or numbness, or even a burning sensation in the affected area
- Muscle weakness and fatigue: a feeling of loss of strength or unexplained tiredness
- Swelling or inflammation of the affected area
It's important to note that MSD symptoms can vary from person to person, and can also evolve over time. If you suspect you are suffering from MSDs, we recommend that you consult a healthcare professional for a precise diagnosis and appropriate treatment plan.
Employer obligations regarding MSDs
Articles L 4121-1 to -5 of the French Labour Code state that the employer is responsible for :
- preventing occupational hazards
- providing information and training
- setting up appropriate organization and resources
What are the prevention principles to be observed?
- Avoid risks
- Assess risks that cannot be avoided
- Combat risks at source
- Think about workstation ergonomics
- Minimize operator discomfort, fatigue and strain
- Make work less dangerous
- Implement prevention
- Take collective protection measures
- Give clear instructions
Source : https://travail-emploi.gouv.fr/
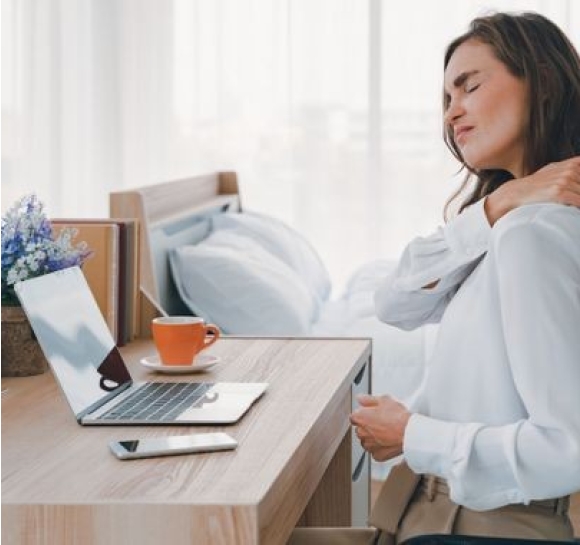
What are musculoskeletal disorders?
MSDs are illnesses often linked to working conditions. All companies and all sectors of activity are concerned. It's the 1st cause of occupational illness
It's a major risk that every employer needs to take into account. In fact, in 2015, they accounted for 87% of occupational illnesses resulting in time off work or financial compensation, and over the past 15 years they have increased by 60%.
There are many causes: repetitive movements, intense or excessive physical effort, screen work, lack of mobility... Mechanical vibration and cold also amplify the risk of MSDs. The fast pace of work, high expectations and lack of recognition at work can lead to stress and muscular pain.
Reducing work-related stress improves employee well-being, which in turn has a beneficial effect on quality of work, absenteeism and productivity.
How to reduce workstation-related MSDs and manual handling?
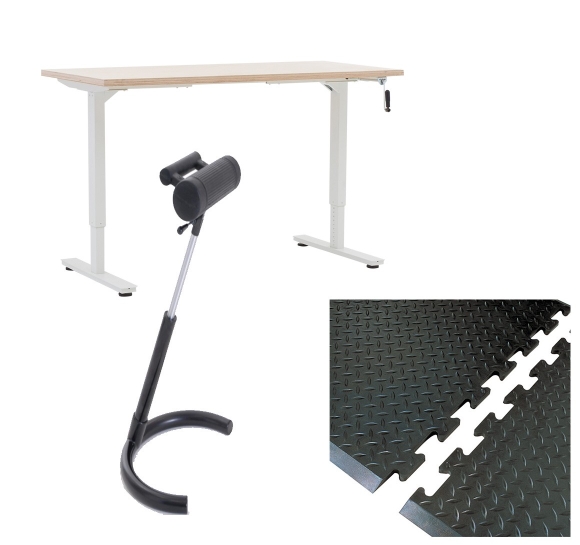
Efficient workstation layout
Several criteria must be taken into account when designing a workstation:
- Frequency and duration of operations or treatments to be carried out
- Volume of objects to be handled
- The size of the work area
- The need to supply or evacuate products, the need to move around, etc
To combat MSDs, you need to take these criteria into account to define the height of the work surface and the most appropriate seating method to eliminate constraints.
Legislation requires employers to safeguard the mental and physical health of their employees, and to adapt work to people. The employer must provide a workstation and seat adapted to the employee's morphology and tasks. (article L.4121-1)
- Standing: We recommend the use of anti-fatigue mats to limit heel shock due to static posture and relieve an uncomfortable position. It reduces muscular fatigue and improves production quality.
- Sit-stand: A sit-stand chair allows you to work with support, and reduces the strain of working in a standing position. We offer a range of models with tubular, sloping or horseshoe bases. For safety reasons, the legs are fixed to prevent falls.
- In variable-height positions: We offer height-adjustable industrial workstations or benches. Our modular workshop workstations allow you to adjust the height to suit the person's morphology and the task in hand. Ideal for handling heavy and bulky products.
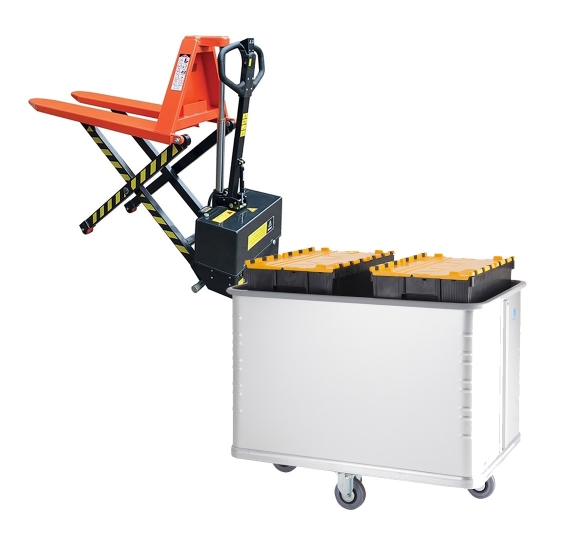
Reduce the risks associated with manual handling with adapted forklifts and pallet trucks
Carrying, pushing, pulling, lifting, placing or depositing loads involves physical effort and sometimes uncomfortable working positions.
Carried out at a fast pace, or in a repetitive manner, these handling operations can cause accidents, fatigue, pain or primary illnesses. Inadequate management of these conditions can compromise job retention.
High-lift pallet truck: to reduce the strain of these operations, we offer you several handling aids, such as the high-lift pallet truck with raised rolling platform, for easy lifting and ergonomic levelling of heavy loads.
Constant-level cart: for repetitive handling operations, we recommend the use of a cart with a movable floor to maintain a constant height. The cart's platform raises or lowers according to the weight of the contents being transported. Operators can thus load and unload without repeatedly bending down.
Legislation and standards on manual handling
When it comes to manual handling, you need to comply with legislation that sets regulatory limits for the manual carrying of loads. As a general rule, workers may only be allowed to carry loads in excess of 15 kg if they have been found fit to do so by the occupational physician. Under no circumstances may loads carried exceed 25 kg, subject to certain conditions. For young workers, limits depend on age and sex.
French standard NF X35-109, on ergonomics in manual load handling, defines reference threshold values, applicable to men and women aged 18 to 65 without distinction. The maximum acceptable value applies when it appears that manual handling operations cannot be eliminated.
The conditional maximum value applies when mechanical lifting and transport aids are difficult to install, due in particular to the configuration of the premises.
Ergonomic threshold values for load handling :
Activity | Maximum acceptable value | Conditional max value |
Lifting Carrying | 15 kg load per operation and 7.5 tonnes / day | 25 Kg load per operation and 12 tons / day |
Push pull | 200 kg weight moved | 400 kg of weight moved |
RSI related to storage equipment: risks and solutions
In the world of warehouses and distribution centers, efficiency and space optimization are key concerns. However, in the quest to save space, many managers resort to practices that can have serious long-term consequences for operators.
To reduce these risks while maintaining efficient logistics, solutions exist: from a review of logistics organization with an increase in the surface area dedicated to order picking, to innovations such as dynamic storage or inclined shelves and racks, and even the introduction of pallet drawers. In addition to improving working conditions for operators, these approaches can sometimes even further optimize storage space.
Let's dive into this world of logistics optimization, where operator safety and efficiency go hand in hand.
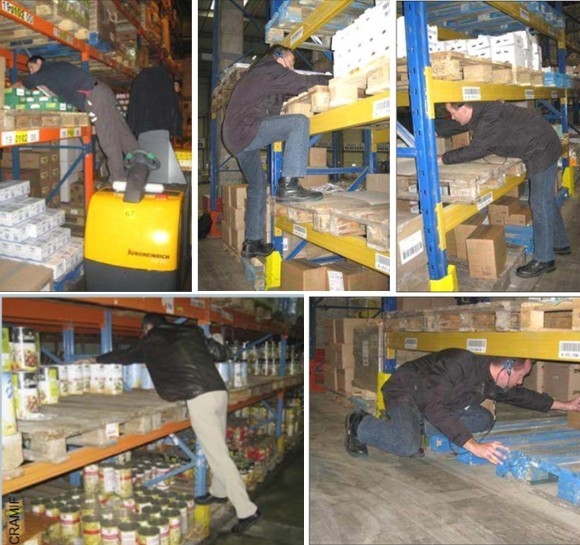
High-risk work situations in warehouses
The constant need to optimize storage space is leading warehouse managers to divide the storage areas used for order picking into 2 or 3 levels. This practice requires physical effort and awkward postures when picking items.
Items stored on the floor: pickers have to bend, crouch or kneel to get under the bottom rail. Then they have to carry the products back to the aisle, completely off-balance, while taking care not to hit their heads on the top rail/pallet!
Items stored at height: To access them, pickers must either :
- Reach out (which strains the lumbar discs);
- Climb onto an unsuitable support (pallet truck, intermediate shelf, parcel...) for the most distant items, which exposes them to the risk of falling.
Long-term consequences for the operator :
- Work-related accidents: lumbago, shoulder pain, banging head against rail, falls, etc
- Occupational illnesses (RSI)
How can these risks be reduced? Prevention methods and solutions:
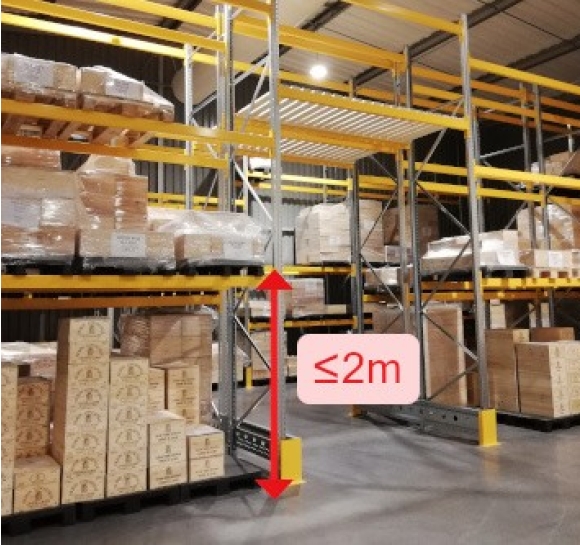
Review of logistics organization
Here are several solutions for eliminating these double and triple storage levels:
- Reduce the number of picking items in the same area;
- Increase the surface area dedicated to order picking (optimize available space, extend the warehouse, rent additional space/overhang, etc.);
- Partial replacement of order picking through splitting, allotment and cross-docking.
To ensure that your employees benefit fully from this approach, you also need to put in place :
- A minimum height of 2 m for beams (to avoid head impacts)
- Standard locations with pallets raised by 0.40m (eliminates the need to pick up parcels in a very low position)
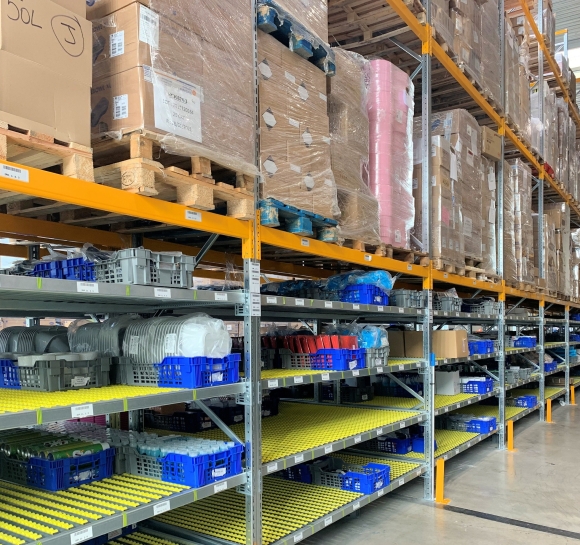
Dynamic storage
This system enables a large number of SKUs to be stored, and items to be easily retrieved from the front. 12 SKUs stored on double-deck pallets are equivalent to between 24 and 32 SKUs stored dynamically.
No loss of storage space! This equipment fits easily under storage pallets.
Products are lowered by gravity onto steel rollers, so there's no longer any problem with gripping depth. Supply is from the rear, for FIFO (First In First Out) storage.
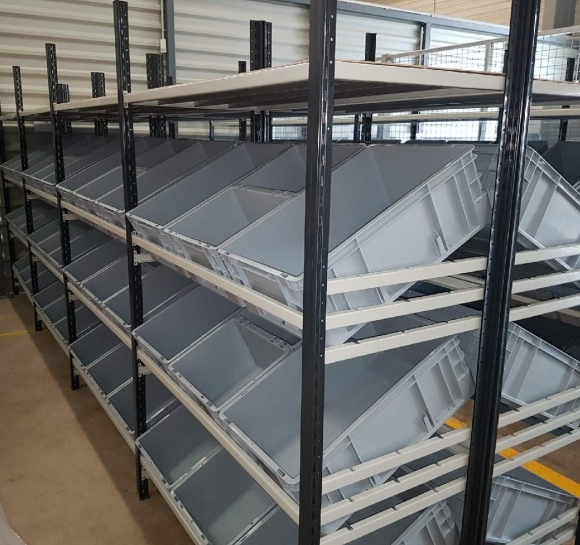
Inclined shelves and racks
This system, dedicated to slow-moving, space-saving items, can store a large number of items.
As with dynamic storage, Provost offers you the option of inserting this system underneath your pallet racking. The inclined position allows rapid visualization of stock levels and picking of items.
For operator comfort, these criteria must be respected:
- Picking depth ;
- Picking height between 0.50 and 1.50m
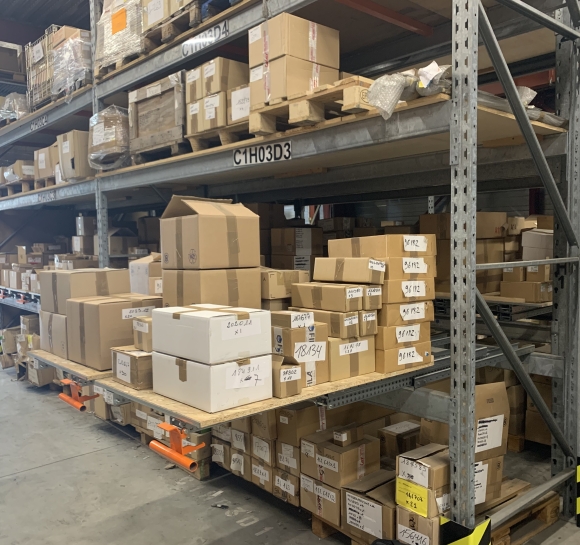
Pallet drawer
Picking is greatly facilitated by this pallet drawer, which extends completely out of the storage area, allowing access to all stored loads.
Without mechanical assistance, the operator has access to all sides of the drawer for better organization and stock location.
Reduced workload: With this storage system, employees no longer have to bend over to access products. Goods are easily accessible from two or three sides.
Space-saving: Drawers optimize the layout of your storage areas according to your products. They offer the flexibility of stacking several levels without wasting space, speeding up the picking process and enabling multiple items to be stored on a single pallet.
Enhanced safety: The use of pallet drawers favors manual handling of goods, reducing the movement of motorized vehicles close to handlers.
Finance your prevention project
TMS PROS DIAGNOSTIC, finance training and the implementation of an action plan:
With a ceiling of €25,000, this aid against the risks of musculoskeletal disorders can finance 70% (before tax) of the cost of one or more of the following services:
- Training of an internal resource person or prevention officer, to enable him/her to lead and implement a musculoskeletal disorder prevention project within the company;
- An ergonomic study of work situations to produce an MSD prevention diagnosis and action plan.
TMS PROS ACTION, finance the purchase of materials and equipment
TMS Pros Action enables you to purchase materials and/or equipment to reduce physical constraints, particularly when handling loads manually, making repetitive efforts or using awkward postures.
It can also be used to carry out training programs for the employees concerned. With a ceiling of €25,000, TMS Pros Action will finance 50% of this type of investment, exclusive of tax, with a minimum of €2,000.
Are you interested in these grants? Would you like more information? Contact your regional CARSAT!
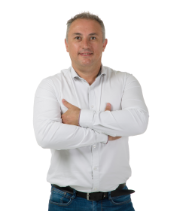